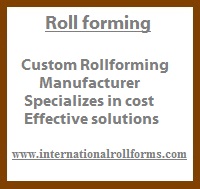
Roll forming machines can produce many cross section profiles. However, they require a crafted set of roll tools for that. The materials that are designed are not heavy yet extremely strong. Finishing or paint is not necessary for these products. These kinds of machines can process in a number of methods. These processes include flat rolling, ring rolling, foil rolling, controlled rolling and roll bending. They are also used to minimize the usage of a new set of roll for producing similar materials like track profiles and studs.
Many different types of materials are used in the process. It is possible to manufacture a wide variety of roll formed parts and shapes. A majority of metals that exist can be roll formed. Complex parts and shapes can be made from basic cold roll steel to per-coated material to vinyl-laminated material with minimal complications to worry about.
Some of the industries that are known to use Roll form parts include automotive, construction, home appliances, marine, medical, aerospace, agricultural and energy. Trim, door panels, roofing, framing studs, siding, and gutters are some common products used in the construction industry. Rails, channels, angles, tubing, C, Z and T shapes are common shapes that are used in a number of different industries for various purposes.
There are a few precautions that need to be taken when designing a project. To avoid marring of the surface, lubrication will be needed. Cold working of the metal can harden it and make it brittle or susceptible to splitting in tight corners. A fluid rolling pattern can alleviate unnecessary stresses. These should be kept in mind during the process of roll forming.